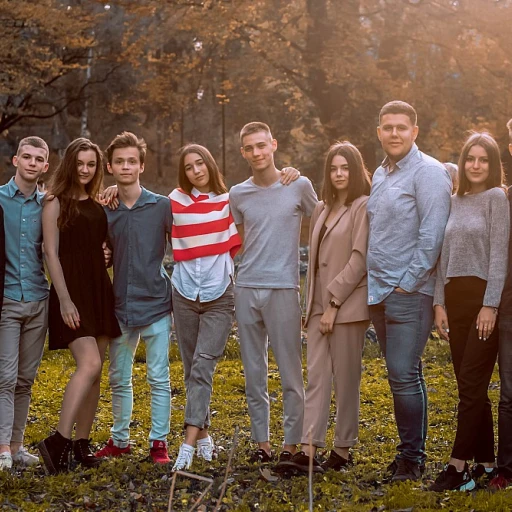
Understanding Continuous Improvement Certification
Understanding the intricacies of a comprehensive Continuous Improvement Certification program can significantly influence an organization's corporate culture. At its core, this certification process entails a meticulous study and application of proven methodologies geared towards sustainable change and enhanced productivity.Delving into the Basics of Certification
With an array of available certifications ranging from Lean to Sigma, Green Belt to Black Belt, this training equips professionals with the necessary skills to drive process improvement and project management within their sectors. These courses offer a wealth of knowledge in disciplines like business process mapping, quality management, and change management strategies.The Essentials of Continuous Improvement
A Continuous Improvement Certification emphasizes on instilling principles of Lean Manufacturing and Lean Sigma into various business processes. The aim is to create a culture where quality management and efficiency are paramount, encouraging professionals to prioritize processes that are both effective and economical.The Role of Quality and Analysis
Central to these certification programs is the focus on quality enhancement and thorough analysis. Through comprehensive online training, managers are prepared to improve operational processes, streamline supply chains, and refine project management. Furthermore, an improvement specialist's expertise can revolutionize the standard management practices. For more insights on how such certifications can mold a thriving corporate environment, you may explore Enhancing Corporate Culture with Agile Brain Consulting for further reading and resources.The Role of Certification in Shaping Corporate Culture
The Transformative Potential of Certification in Company Culture
In the modern business landscape, certification programs such as Lean and Sigma play a crucial role in shaping corporate culture. At the core of this transformation is the commitment to continuous improvement, a philosophy that fosters a growth mindset among employees and managers alike. By pursuing a structured certification course, organizations send a clear message about their dedication to quality management and process enhancement. Certifications serve as a guiding light for businesses striving to instill a culture of excellence. When employees engage in training such as Lean Sigma, they learn to embrace effective project management and business process optimization techniques. This in turn enhances their ability to contribute meaningfully to the organization’s goals.Benefits of Continuous Improvement Certification for Employees
Empowering Employees through Enhanced Skills and Knowledge
The pursuit of improvements is an ongoing endeavor in any thriving business environment. Continuous improvement certification plays a pivotal role in this process by equipping employees with the necessary skills and knowledge. This development not only aligns with lean and six sigma methodologies but also broadens employees' horizons through specialized training and courses such as lean manufacturing, black belt, and green belt certifications. Employees who undergo these programs emerge as valuable assets capable of driving improvements across various domains of the organization. By understanding quality management principles and applying project management strategies, employees can actively participate in refining business processes and elevating manufacturing procedures. This involvement does more than just bolster operational efficiency—it empowers employees to take ownership of projects, fostering a sense of accomplishment and purpose in their work. For insights on this connection, explore finding purpose in your work. Moreover, with tailored improvement specialist and manager certification courses, staff are more adept at implementing change. These certifications focus on essential process mapping and sigma green methodologies, enabling employees to conduct deep analysis and craft strategies for continuous refinement. Organizations benefit from having a workforce trained in these areas as it promotes a culture of self-development and proactive problem-solving, critical for sustaining competitive advantage. Through such certifications, employees not only gain technical expertise but also become integral contributors to the company's strategic goals. Their commitment to ongoing education reflects a culture that values growth and adaptation, qualities that are invaluable in today’s rapidly evolving business landscapes.Implementing Continuous Improvement Strategies in the Workplace
Integrating Continuous Improvement into Daily Operations
Implementing continuous improvement strategies in the workplace involves more than just attending a course or obtaining a certification. It requires a shift in mindset and a commitment to ongoing development. To effectively integrate these strategies, businesses need to embed them into their daily operations.
Developing a Structured Program
A structured program is essential for successful implementation. This includes defining clear objectives and aligning them with the company's overall goals. Managers should focus on creating a roadmap that outlines the steps needed to achieve these objectives. This roadmap should include key elements such as process mapping, quality management, and change management.
Training and Certification
Training is a critical component of any continuous improvement initiative. Offering courses in lean manufacturing, lean sigma, and project management can equip employees with the necessary skills. Certifications such as green belt, black belt, and sigma master can further enhance their expertise. Online certifications provide flexibility and accessibility, making it easier for employees to participate.
Engaging Employees in the Process
Employee engagement is crucial for the success of continuous improvement strategies. Encouraging employees to take ownership of their roles and contribute ideas for process improvement can foster a culture of innovation. Improvement specialists and improvement managers can facilitate workshops and brainstorming sessions to gather input and drive change.
Monitoring and Analysis
Continuous improvement is an ongoing process that requires regular monitoring and analysis. Businesses should establish metrics to evaluate the effectiveness of their strategies. This involves conducting regular reviews and using data analysis to identify areas for further improvement. By doing so, companies can ensure that their efforts are yielding the desired results.
Leadership and Support
Leadership plays a pivotal role in the successful implementation of continuous improvement strategies. Managers must lead by example and provide the necessary support to their teams. This includes offering guidance, resources, and recognition for achievements. A supportive leadership team can motivate employees to embrace change and strive for excellence.
Challenges in Adopting Continuous Improvement Certification
Overcoming Hurdles in Adopting Certification Programs
The journey toward adopting Continuous Improvement Certification within an organization is laden with challenges that can impede successful implementation. Companies must navigate these obstacles effectively to reap the full benefits of process optimization and quality management. First, resistance to change is a significant issue. Introducing new methodologies like lean manufacturing or sigma green practices often disrupts established workflows, prompting hesitation among team members. Change management becomes crucial in easing transitions and fostering an environment receptive to new quality management strategies. Another challenge involves the initial costs and resources required for training. Organizations may need to invest in comprehensive courses to equip employees with the requisite certifications, such as black belt or improvement specialist. These certified quality courses often entail substantial financial backing and time commitment, both for training sessions and knowledge application. Additionally, aligning certification goals with organizational objectives can pose a difficulty. Continuous improvement managers must ensure that the newly adopted systems are aligned with existing business processes. This alignment requires diligent process mapping and analysis to integrate certification programs seamlessly with the company's strategic vision. Moreover, realizing substantial benefits from lean sigma certifications and quality management practices demands a cultural shift within the organization. This shift encourages employees to embrace continuous improvement mindsets by valuing efficiency and project management's role in driving change. Sharing success stories of peers or industry exemplars can also help mitigate doubts. By showcasing practical examples of lean sigma certifications enhancing business process and encouraging program adoption, organizations can build credibility and trust among team members.Case Studies: Success Stories of Continuous Improvement Certification
Success Stories Through Practical Applications
Organizational success in continuous improvement certification can often be attributed to the application of lean and sigma principles. These methodologies, which focus on efficiency and quality management, have been pivotal for many industries, including manufacturing and supply chain. By implementing these strategies, companies have seen significant transformations in both their corporate culture and bottom-line results.
A notable example of successful implementation can be seen in the manufacturing sector, where continuous improvement courses have become integral to training programs. Employees taking courses in lean sigma and process mapping are better equipped to handle the challenges of modern production environments. Organizations that have integrated such courses as part of their certification programs notice employees achieving green and black belt statuses are often promoted to key management roles, such as improvement specialist or project manager.
Those undergoing certification programs report increased job satisfaction due to the enhanced ability to contribute meaningfully to business process improvements. A continuous culture of learning and growth is cultivated within these companies, which in turn fuels overall business success and a robust corporate culture. Continuous improvement not only helps in refining processes within operational departments but also influences management strategies, leading to a more engaging work environment.
Additionally, businesses that invest in such programs notice improvements in their process management and quality management systems. By focusing on both the technical aspects of improvement and the human aspects, including change management initiatives, companies have succeeded in fostering an environment where innovation can thrive.
Such case studies emphasize the vital role that continuous improvement certification plays in evolving corporate culture into one that prioritizes quality and adaptation. This transformation requires commitment and consistency, yet the rewards are clear in the form of heightened employee engagement, process efficiency, and enhanced organizational reputation.